可製造性設計:為精益生產、按單生產和大規模定製設計產品 | 生病了怎麼辦 - 2024年7月
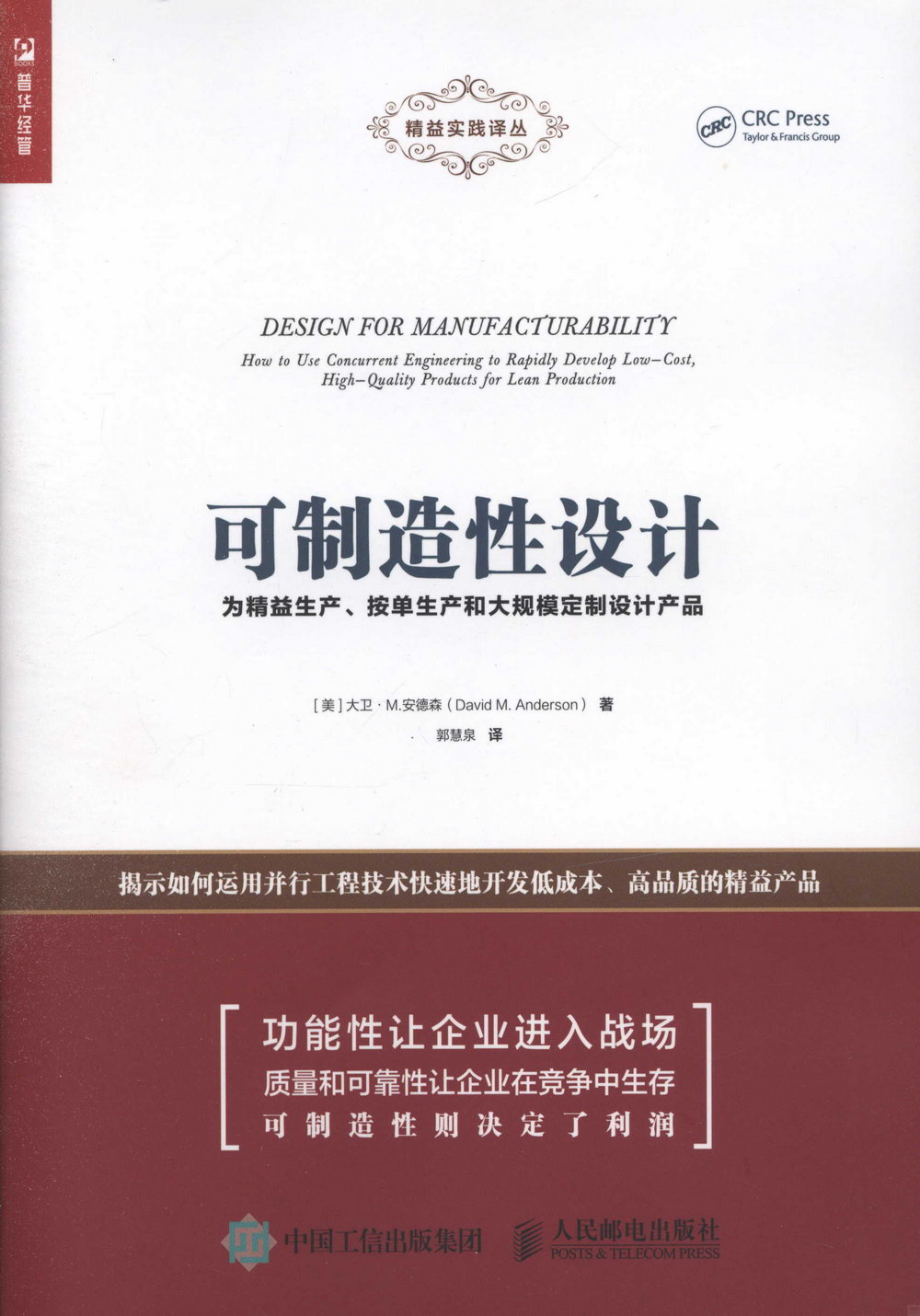
可製造性設計:為精益生產、按單生產和大規模定製設計產品
如何以精益生產、按單生產和大規模定制為基礎設計產品系列?產品生產過程中各流程的設計準則有哪些?如何運用各項品質準則進行產品的可靠性設計?本書對以上問題進行了詳細解答,介紹了企業在產品製造的每個流程中如何通過多功能型團隊合理運用並行工程技術,實現低成本、高品質以及快速達到穩定生產的目標。
作者根據其數十年來在工業領域的設計和製造經驗,將可製造性設計的理念擴展為一個產品開發模型,同時闡述了在實現各個產品開發目標的過程中,如何有效地貫徹精益生產和各類品質方案,全面、同步地作出關鍵性的改善。作者還針對各類產品開發實例、培訓和管理方法提出了優化建議,概述了零件和材料標準化的有效程序、節約時間和成本的方法以及執行標準化方案的措施。
本書適合產品研發工程師、團隊負責人、生產管理者、專案與研究開發部經理、行銷和投資組合規劃人員及投資者閱讀,也可作為大學教材、相關研究機構的參考讀物,以及公司內部的培訓資料。
大衛·M.安德森博士是運用並行工程技術進行可製造性設計的國際專家。在過去20多年中,安德森舉辦了一系列與可製造性設計相關的內部專業研討 會,總結並提煉出了各種方法論,幫助諸多企業有效地提高了穩定生產的速度並顯著地降低了總成本。
安德森在工業界擁有超過35年的設計和製造經驗。他創建的 安德森自動化公司(Anderson Automation Inc.)致力於為各大製造公司進行設計研究。該公司建造了適用於IBM的生產設備。安德森憑借其在並行工程技術方面的經驗,在自己的加工車間建造了他自 主研發設計的設備。他已經獲得了四項專利,並且還在研發新的產品。
安德森是美國機械工程師協會(American Society of Mechanical Engineers,ASME)的研究員、製造工程師協會(Society of Manufacturing Engineers,SME)的終身會員,以及管理顧問協會(Institute of Management Consultants)認證的管理顧問。他還在加州大學伯克利分校的技術管理項目中,編寫了產品開發課程的教材,並教授該課程。
引言
本書綱要
寫給讀者的話
第 一部分 設計方法
第 1 章 可製造性設計
1.1 DFM 出現之前的製造業
1.2 產品開發的誤區和現實
1.3 實現最低成本
1.4 低成本設計
1.5 讓上市時間減半
1.6 角色和管理重點
1.7 DFM 面臨的阻礙
1.8 武斷決策
1.9 DFM 和設計階段
1.10 工程變更
1.11 一次成功
1.12 一次成功的策略
1.13 DFM 為企業帶來的好處
1.14 DFM 為個人帶來的好處
1.15 結論
1.16 注釋
第 2 章 並行工程
2.1 資源的獲得
2.2 確保資源的可獲得性
2.3 產品組合規劃
2.4 平行產品和未來產品
2.5 團隊作為整體設計產品
2.6 與供應商 / 合作夥伴的關係
2.7 團隊負責人
2.8 同地辦公
2.9 團隊成員和角色
2.10 工程外包
2.11 產品定義
2.12 注釋
第 3 章 設計產品
3.1 設計策略
3.2 全面的前期工作的重要性
3.3 架構優化和系統設計
3.4 零件設計策略
3.5 面向各個環節的設計
3.6 產品創新
3.7 頭腦風暴
3.8 成本減半的產品開發
3.9 注釋
第二部分 柔性
第 4 章 為精益生產和按單生產進行設計
4.1 精益生產
4.2 按單生產
4.3 大規模定制
4.4 為精益生產、按單生產和大規模定制開發產品
4.5 為精益生產、按單生產和大規模定制規劃產品組合
4.6 為精益生產、按單生產和大規模定制設計產品
4.7 模組化設計
4.8 離岸外包和可製造性
4.9 精益化按單生產和大規模定制的價值
4.10 注釋
第 5 章 標準化
5.1 零件激增
5.2 零件激增的成本
5.3 零件為什麼會激增
5.4 零件激增的後果
5.5 零件標準化策略
5.6 標準化的早期步驟
5.7 從零開始的策略
5.8 生成標準件列表
5.9 零件標準化結果
5.10 原料標準化
5.11 昂貴零件標準化
5.12 合併非柔性零件
5.13 工具標準化
5.14 特徵標準化
5.15 工藝標準化
5.16 鼓勵標準化
5.17 重用已有的設計、零件和模組
5.18 現貨零件
5.19 採購的新角色
5.20 實施標準化
5.21 注釋
第三部分 降低成本
第 6 章 通過設計最小化總成本
6.1 為什麼不能降低成本
6.2 成本統計
6.3 使成本減半的策略
6.4 通過設計使成本最小化
6.5 最小化間接成本
6.6 最大限度地降低產品開發成本
6.7 現貨零件對節約成本的貢獻
6.8 最大限度地降低工程變更成本
6.9 最大限度地降低品質成本
6.10 合理選擇成本最低的供應商
6.11 低價投標
6.12 最大化工廠效率
6.13 利用柔性降低間接成本
6.14 最小化定制 / 配置成本
6.15 最小化品種多樣化成本
6.16 最小化物料管理成本
6.17 最小化行銷成本
6.18 最小化銷售 / 分銷成本
6.19 最小化供應鏈成本
6.20 最小化產品生命週期成本
6.21 通過按單生產來節約成本
6.22 造成負面效應的成本降低措施
6.23 注釋
第 7 章 總成本
7.1 總成本的價值
7.2 量化間接成本
7.3 總成本核算的障礙
7.4 總成本思維
7.5 實施總成本核算
7.6 成本驅動要素
7.7 跟蹤產品開發費用
7.8 abc:低目標的作業成本法
7.9 實施工作 // 265
7.10 實施總成本策略的典型結果
7.11 注釋
第四部分 設計準則
第 8 章 產品設計的 DFM 準則
8.1 裝配設計
8.2 裝配設計的指導準則
8.3 緊固準則
8.4 動態裝配準則
8.5 測試策略和準則
8.6 品質測試與在製造中控制品質
8.7 維修和保養設計
8.8 維修準則
8.9 服務與維修設計
8.10 維護
8.11 維護的測量指標
8.12 維護準則設計
8.13 注釋
第 9 章 零件設計的 DFM 準則
9.1 零件設計準則
9.2 成品零件的 DFM 準則
9.3 鑄件和模壓件的 DFM 準則
9.4 金屬板材的 DFM 準則
9.5 焊接的 DFM 準則
9.6 大型零件的 DFM 準則
9.7 注釋
第五部分 客戶滿意度
第 10 章 品質設計
10.1 品質設計準則
10.2 公差
10.3 產品品質的累積效應
10.4 可靠性設計準則
10.5 可靠性測量
10.6 各個階段的可靠性
10.7 防錯技術
10.8 防錯準則
10.9 品質設計策略
10.10 客戶滿意度
10.11 注釋
第六部分 實施
第 11 章 實施 DFM
11.1 變更
11.2 初步調查
11.3 DFM 培訓
11.4 DFM 工作組
11.5 停止使用會帶來反效果的策略
11.6 企業執行
11.7 團隊執行
11.8 個人執行
11.9 學生和求職者與 DFM
11.10 DFM 的主要任務、結果和工具
11.11 結論
11.12 注釋
第七部分 附錄
附錄 A 產品線合理化
A.1 產品線的帕累托法則
A.2 合理化如何帶來三倍利潤
A.3 通過合理化節約成本
A.4 把重點轉向最有利可圖的產品
A.5 合理化策略
A.6 合理化過程
A.7 總成本影響
A.8 克服顧慮、恐懼和抗拒心理
A.9 企業策略實踐
A.10 合理化如何提高企業品質
A.11 合理化的價值
A.12 注釋
附錄 B 準則概要
B.1 裝配策略準則(第 8 章)
B.2 緊固準則(第 8 章)
B.3 動態裝配準則(第 8 章)
B.4 測試準則(第 8 章)
B.5 修理準則(第 8 章)
B.6 維護準則(第 8 章)
B.7 零件設計準則(第 9 章)
B.8 成品零件的 DFM 準則(第9章)
B.9 鑄件的 DFM 準則(第 9 章)
B.10 塑膠工藝的 DFM 準則(第 9 章)
B.11 金屬板材的 DFM 準則(第 9 章)
B.12 品質設計準則(第 10 章)
B.13 可靠性設計準則(第 10 章)
附錄 C 回饋表
附錄 D 參考資料
D.1 參考書目
D.2 提高企業運營的隨身指南
D.3 DFM 研討會
D.4 BTO 和大規模定制的研討會
D.5 安德森博士創辦的研討班
D.6 設計研究與諮詢